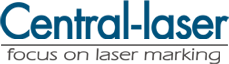
Release time:2020-10-28 viewed:11
In recent years, the application of laser technology in the automotive industry has become increasingly common. In terms of technology, laser marking, hardening, cutting, welding, laser headlights, laser radar and so on are all used. In terms of parts, all kinds of inside and outside, up and down, structural decoration and so on are all used. Laser can be seen everywhere in a car. It can be said that there is no car without laser.
Application of laser in car body processing
According to relevant statistics, 50% - 70% of auto parts in developed industrial countries in Europe and America are processed by laser. We also make a preliminary analysis of the application of laser in automobile manufacturing.
Laser welding
Laser welding has the following characteristics:
① The heating range is narrow (concentrated).
② The area and position of working can be controlled accurately.
③ The heat affected zone is small.
④ The welding deformation is small and no need for postweld correction.
⑤ Non contact processing, without pressure and surface treatment.
⑥ It can realize dissimilar material welding.
⑦ The welding speed is fast.
⑧ No heat effect, no noise and no pollution.
The diameter of laser beam irradiating on the material surface is 0.2-0.6 mm, and the weld width is less than 2 mm. After rapid solidification, the crystalline grains of laser welded metal are finer and higher strength can be obtained. Laser welding can increase the rigidity of the car body by 30%. Compared with the traditional spot welding process, the laser welding of the roof cover and the side wall has two less rubber sealing strips, which improves the visual effect of the car body. The "one millimeter project" in the precision control of body (the dimension precision of body in white is controlled within ± 1 mm) is realized by laser welding.
Laser welding accelerates the process of replacing forging parts with stamping parts. Using laser welding, continuous laser welding instead of discrete spot welding, can reduce the lap width and some strengthening parts, can compress the volume of the body structure itself. As a result, the body weight can be reduced by 56kg. The application of laser welding realizes weight reduction and emission reduction, which meets the requirements of environmental protection in present era.
When laser welding is applied to welding of unequal thickness plates, the benefit is more remarkable. This technology transforms the traditional manufacturing process -- first stamping into parts, and then spot welding into a whole -- into: first welding several parts of different thickness into a whole, and then stamping forming, which reduces the number of parts, makes more reasonable use of materials, and significantly improves the structural function.
Laser welding can also be applied to cigarette lighter, valve tappet, cylinder pad, fuel nozzle, spark plug, variable speed gear, half shaft, transmission shaft, radiator, clutch, engine exhaust pipe, turbocharger axle, airbag liner, ABS, etc.
Laser cutting
Laser cutting was used in the manufacture of automobile parts earlier.
The laser cutting of automobile large panel, such as cutting edge and wind shield, needs 3D cutting machine or robot. Flexible cutting system composed of robot and fiber laser is common.
In recent years, high strength steel has become the main lightweight material in automobile industry due to its advantages of high weight reduction potential, high impact absorption energy, high fatigue strength, high formability and low plane anisotropy. After hot forming of high strength steel, the stamping process is no longer suitable, and the cutting of its contour and hole promotes the demand for laser cutting.
Automotive interior parts are mostly non-metallic. Because of the characteristics of laser, such as non-contact, accurate positioning, fast and so on, it is very suitable for laser cutting. For example, the waste corner material of the door panel or door shoulder and the surplus part of the rear injection molding parts are cut off. Cutting nonmetal can't use fiber laser, but must use CO2 laser, without the convenience of fiber laser transmission, the matching robot must be specially designed, the CO2 laser beam guiding device is fully integrated in the robot arm, so that the moving robot arm can transmit stable laser beam.
Laser marking
The traditional marking methods of auto parts include: mold casting, electric corrosion, non-drying glue, silk screen printing, pneumatic marking, etc. Laser marking technology has been developing rapidly with its clear and beautiful marking since its birth.
The advantages of laser marking for auto parts are: fast, programmable, non-contact and durable. Laser marking is widely used in automobile manufacturing, such as automobile parts, engine, label paper (flexible label) and so on. Laser bar code and two-dimensional code are often used in auto parts traceability. Two dimensional code has the advantages of large information capacity and strong fault tolerance.
The special laser marking machine for automobile flexible label is specially designed according to the characteristics of automobile flexible label. It is used for marking the following kinds of labels: body, engine, VIN code, bar code, car key, fuel tank, airbag warning, tire pressure, air conditioning, cooling system, door label, etc.
The above is a summary of the application of laser technology in the automotive industry.The importance of laser in automobile industry is more and more prominent, and it affects our daily life more and more widely.
Laser headlamp makes car more dazzling
Laser headlamp is not a strange term. Laser is used in many fields of society. In car design, BMW first proposed to use laser headlamp and apply it to BMW I8. Now the new generation of BMW 7 series can also be equipped with optional laser headlamp. In addition, light playing expert Aodi also launches its laser headlamp.
Laser headlamp has three characteristics: small, bright and far.
Although the appearance of laser headlamp is similar to that of LED headlamp, the connotation is different. The component size of laser diode is only one percent of that of LED, which means that the future lamps will have more different shapes.
The luminous efficiency of LED is 100 lumens per watt, while the laser headlamp carried by BMW I8 can reach 170 lumens per watt. In this way, the laser headlamp can either achieve high brightness or consume less energy under the same brightness.
In addition, the irradiation distance is twice that of LED. However, it is worth mentioning that laser headlamp is mainly used in high beam, low beam is still led.
So is such a strong lighting effect harmful to human body? The answer is No. Because the laser of the laser headlamp is not directly emitted, but first irradiates on a group of reflecting lenses, then emits white light after passing through the yellow phosphorus lens, and finally reflects after another reflection.
Unmanned driving by laser lidar
To achieve partial automatic driving by 2016, for example, the car needs a monitoring system, and the driver needs to be ready to take over driving at any time, with the goal of achieving automatic driving within 30km/h. To achieve highly automatic driving by 2020, when the monitoring system is not needed, but the driver needs to take over driving within the specified time. To achieve fully automatic driving by 2025, the driver does not need a monitoring system, and the driver needs to be fully autonomous. There's no need to take over driving. This is a three-step innovation from assisted driving to automatic driving launched by continental. In fact, this also represents the judgment of most foreign-funded parts enterprises. The real sense of automatic driving requires reliable sensors, safe vehicle data, complex system architecture, safety simulation and laws and regulations. In recent years, there are still many technologies need to be broken through to realize automatic driving, but it can be achieved that more functions of ADAS can be realized in the car as soon as possible to achieve safer and more intelligent car driving.
previous posts:
The next article: Fiber laser marking machine becomes industry focus